Since opening its first location in 2008, citizenM has built 12 hotels using modular construction, totaling about 3,000 rooms. Its portfolio includes the first modular high-rise in New York City as well as the first in Los Angeles. “I would love to be second,” joked Menno Hilberts, the company’s former Managing Director of Development. “I'm tired of being the one that has to convince politicians to get on board with this.”
In a recent presentation at HotelSpaces, Hilberts dug deep into the pros and cons of modular construction. While he pushed back against the idea, endorsed by the likes of McKinsey, that "modular is the future", he argued that many industries could nonetheless benefit from the approach—few more so than hotels.
By Frequent Travelers, for Frequent Travelers
Before he discussed modular construction’s future in the hotel industry, Hilberts turned to the past. As he explained, citizenM got into the modular business for that classic reason: dissatisfaction with the status quo. “We started in 2008 in Amsterdam, largely born out of frustration with the current hotel offering,” he said. “We thought, as frequent travelers, we could do better. So we developed a brand by the frequent traveler, for the frequent traveler.”
The citizenM difference is its modular room: a standardized king-size unit in every hotel. As it demonstrates, modular does not mean spare. “It’s like a luxury yacht cabin,” Hilberts said. “Great bed, great shower, the essentials.” What it sacrifices in living space is made up by the hotels’ vibrant common areas, where guests can mingle with their fellow travelers over 24-hour food and beverage offerings.
Just as citizenM hotels provide guests with a simple and elegant experience, modular design also makes for a simpler and more elegant development and construction process. Consider the traditional approach. “It's a world of constant fighting,” Hilberts lamented. “We spend our day fighting over who owns what and who is at fault for which problem. You start with a new team every time, every project is a blank canvas, you really only deliver one-off prototypes. There’s not a lot of consistency.”
“And honestly, if you step back and look at it, they're all pretty bad,” he added. “They're all too expensive, and they take too long. Even the ones on budget and on time really aren't, and they compromise in quality.”
Taking cues from the manufacturing industry, citizenM learned that a modular approach solved many of these problems. It allows for the same team to work on multiple projects, integrate stakeholders from the start, develop long-term relationships with supply chain partners, and improve quality and risk management. In other words, the process allows for an assembly-line approach to hotel construction. “That's really what we wanted to do,” Hilberts said. “Set up an assembly line and just create these new build hotels.”
A Bold Undertaking
While modular construction usually costs as much as traditional, it is generally faster—and it can be even faster and cheaper when you roll out multiple projects simultaneously. “If all you want to do is build one project, keep doing what you're doing,” he said. “But if we can get people together and actually commit an owner, developers, and a brand to work together and do a rollout, that'll be awesome—if we can standardize the product.”
Hilberts noted that other industries can reap the benefits of modular construction too. “If you can envision your product as a collection of Lego blocks that can be put on a truck, you are in business,” he said. “Student housing, urban condos, or small housing would still work.”
The key to success, he added, is ensuring stakeholders are on the same page from the get-go. “If you can't get the funder, the owner, designer, the general contractor, and the modular supplier under one roof—like the manufacturing industry does—and get them to collaborate and share the good, the bad, and the ugly, it's not going anywhere.”
So, does Hilberts think modular construction is the future? Unfortunately, not quite yet. The development landscape is just too chaotic for the time being; citizenM has already gone through 10 different manufacturers “because they keep going out of business,” he said. Until the industry figures out how to control demand and roll out large construction programs, the cost savings in most parts of the country won’t outweigh traditional construction.
“You want a predictable throughput at your factory of, like, 2,000 rooms a year—and that's not at all the way development works,” he explained. “You have to accelerate and stop constantly, and that's killing the modular companies.”
Still, Hilberts has high hopes that modular’s moment will eventually come to the hotel sector. “There’s real opportunities,” he concluded. “It's a bold undertaking, but I'd love to see it happen.”
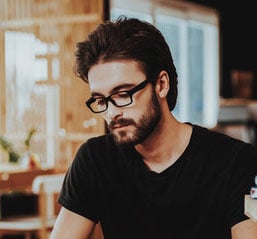
Posted by
Join us at HotelSpaces!
A One of a Kind Retreat for Hotel Development, Design & Construction Leaders.
Nov 2-4, 2025 | Scottsdale, AZ
Learn More
Comments